+86-574 86567814
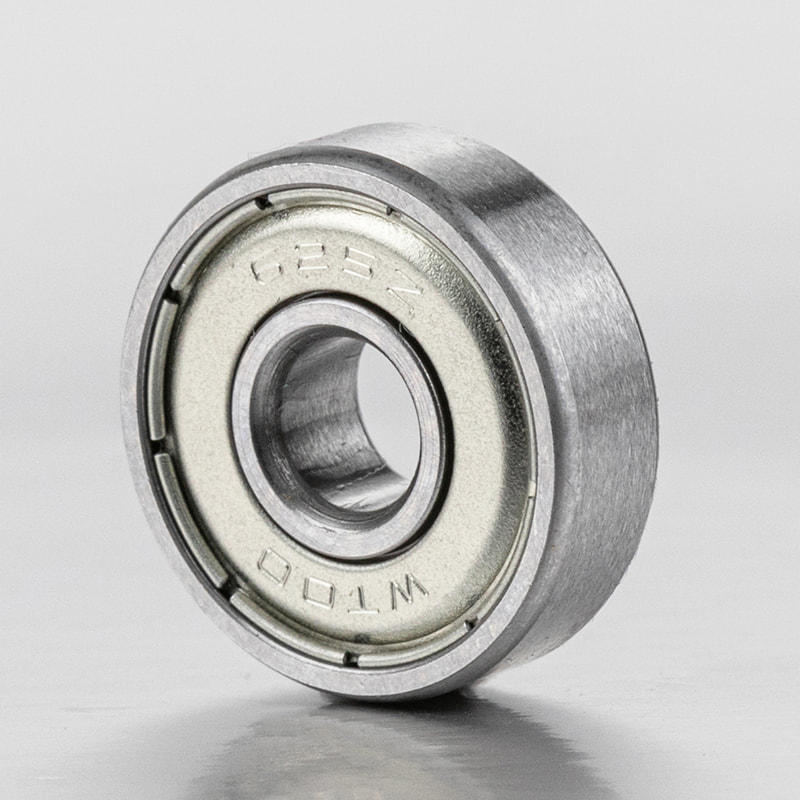
625-Super quiet, high precision, long life deep groove ball bearings
Deep groove ball bearings Deep groove ball bearing...
View moreDeep groove ball bearings Deep groove ball bearing...
View moreDeep groove ball bearings Deep groove ball bearing...
View moreDeep groove ball bearings Deep groove ball bearing...
View more1. Understand the Basic Specifications
Bearing Design: Single row angular contact ball bearings are engineered to handle both radial and axial loads due to their unique design. These bearings feature a contact angle between the balls and raceways, which allows them to support higher axial loads compared to radial bearings. The design also affects the load distribution, with a larger contact angle generally offering greater axial load capacity. Understanding the bearing's design specifications is crucial, as it dictates the bearing's ability to manage the applied loads.
Dimensions: The physical dimensions of the bearing, including the inner diameter (d), outer diameter (D), and width (B), are critical in determining its load capacity. These dimensions influence the bearing's strength and how it distributes loads. Typically, these measurements are provided in detailed technical datasheets from the manufacturer. Ensuring you have accurate measurements helps in selecting the correct bearing size for your application and in performing precise load calculations.
2. Contact Angle Consideration
Impact on Load Distribution: The contact angle, which is the angle between the line of action of the load and the radial plane of the bearing, significantly influences how the bearing handles loads. A larger contact angle means the bearing can support a higher axial load, while a smaller angle favors radial load support. For example, a 15° contact angle is often used for applications with moderate axial loads, while a 25° or 40° angle is suited for high axial loads. Understanding the contact angle is essential for accurately predicting bearing performance under specific load conditions.
Determining Contact Angle: The contact angle is typically specified by the bearing manufacturer and can often be found in the product catalog or datasheet. It is crucial to select a bearing with the appropriate contact angle for your application, as it directly impacts the bearing’s load capacity and performance.
3. Refer to Manufacturer’s Catalog
Load Ratings: Bearing manufacturers provide detailed catalogs that include essential load ratings for their products. These ratings are critical for determining the bearing’s suitability for your application. The catalogs typically include:
Basic Dynamic Load Rating (C): This value represents the maximum load that the bearing can support while rotating, with a standard life expectancy. It is a key indicator of bearing performance and is expressed in newtons (N).
Basic Static Load Rating (C₀): This rating indicates the maximum load the bearing can withstand without permanent deformation when it is stationary. It helps assess the bearing's ability to handle static loads without damage.
Using Catalog Data: To determine the appropriate bearing for your application, consult the manufacturer's catalog to find the relevant load ratings and match them with your application’s load requirements. This ensures that the selected bearing will perform reliably under expected conditions.
4. Use Load Calculation Tools
Software and Calculators: There are specialized software tools and online calculators available that can assist in determining the load capacity of single row angular contact ball bearings. These tools often incorporate detailed formulas, bearing data, and conditions to provide accurate load calculations. Using these tools can simplify the process and ensure precise results.
Advantages of Tools: Load calculation tools help automate the process, reduce the risk of manual errors, and provide quick and reliable calculations based on input parameters. They are particularly useful for complex applications or when dealing with multiple bearings.
5. Consult Engineering Standards
Industry Standards: Engineering standards from organizations such as the International Organization for Standardization (ISO) or the American National Standards Institute (ANSI) provide guidelines and formulas for calculating bearing load capacities. These standards ensure consistency and reliability in load calculations.
Applying Standards: Refer to relevant standards for specific guidelines on load calculations, bearing performance, and testing methods. Adhering to these standards helps ensure that your bearing selection and load capacity calculations are accurate and compliant with industry best practices.
6. Consider Safety Factors
Safety Margins: Including a safety margin in your calculations helps account for unexpected loads, variations in operating conditions, and potential inaccuracies. A typical safety factor ranges from 1.5 to 2 times the calculated load capacity to provide a buffer against potential failures.
Importance of Safety Factors: Safety factors help ensure the bearing operates reliably under varying conditions and extends its service life. They provide additional protection against overloading and help prevent premature bearing failure.