+86-574 86567814
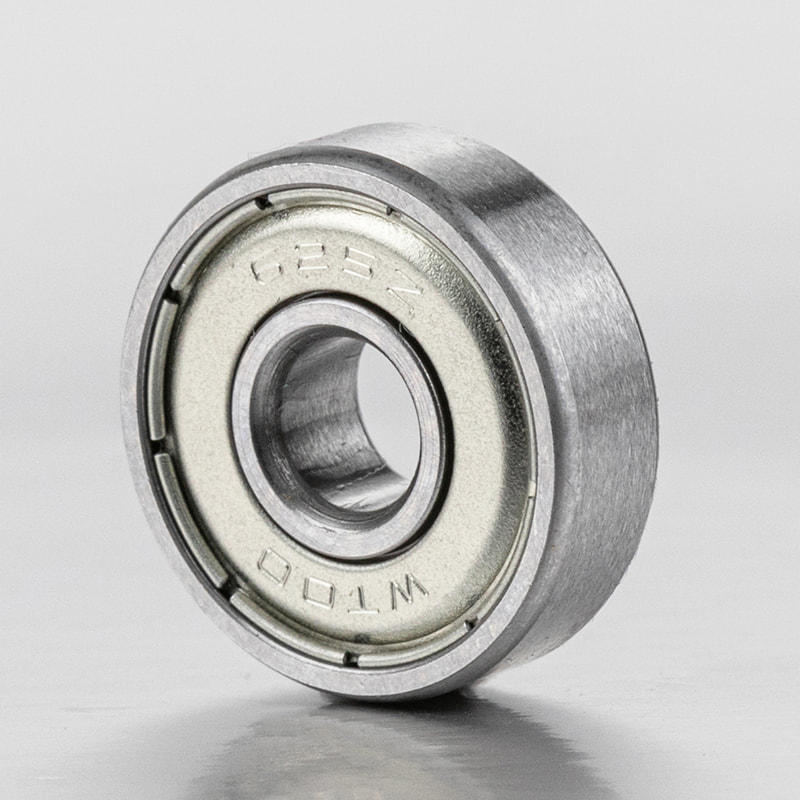
625-Super quiet, high precision, long life deep groove ball bearings
Deep groove ball bearings Deep groove ball bearing...
View moreDeep groove ball bearings Deep groove ball bearing...
View moreDeep groove ball bearings Deep groove ball bearing...
View moreDeep groove ball bearings Deep groove ball bearing...
View more1. Load carrying capacity
Angular contact ball bearings are designed to be optimized for carrying both axial and radial loads. The contact angle of such bearings is usually between 15° and 40°, and the size of the contact angle directly affects its axial load carrying capacity. The larger the contact angle, the greater the axial load the bearing can withstand, so choosing the right contact angle is particularly important in high-load applications. For example, in high-speed, high-load rotating equipment, angular contact ball bearings with larger contact angles are usually selected to ensure that they can still operate effectively under complex load conditions. The design of the inner and outer rings of angular contact ball bearings also takes into account the distribution of loads, reducing stress concentration and thus reducing the risk of fatigue damage. This design enables angular contact ball bearings to operate stably and withstand large operating loads in high-load environments such as machine tool spindles and gearboxes, ensuring the efficiency and safety of the equipment.
2. Stability and reliability
In high-load applications, the stability and reliability of angular contact ball bearings are crucial. Because these bearings are designed with the complexity of loads in mind, they can effectively cope with changes in dynamic loads and maintain good working conditions. High-precision machining and material selection of the inner and outer rings, rolling elements and cages of the bearings ensure low friction and low heat generation characteristics, thereby reducing heat accumulation caused by friction. Excessive temperature may cause the performance of the lubricant to deteriorate, which in turn affects the operation of the bearing, so good heat dissipation performance is essential for high-load applications. Reasonable lubrication methods can further improve stability and ensure long-term reliable operation of the bearing under high load conditions. By monitoring the operating temperature and vibration of the bearings and timely discovering potential problems, the equipment failure rate can be effectively reduced and the equipment life can be extended.
3. Reduce vibration and noise
In high-load applications, the vibration and noise of the equipment are usually large, and the design of angular contact ball bearings helps to reduce these adverse effects. This type of bearing is manufactured with high precision and good fit, which can effectively reduce imbalance and vibration during operation. High-frequency vibration not only causes mechanical fatigue, but also affects the performance of other components and increases maintenance costs. Therefore, choosing the right angular contact ball bearing can greatly reduce the noise during equipment operation and provide a more comfortable operating environment. By optimizing the geometry of the rolling elements and lubrication conditions, the bearing runs more smoothly and reduces the sound caused by friction. Good shock absorption performance can improve the stability of the entire system and enable the equipment to maintain good working condition under high load conditions. This is crucial for many industrial applications, such as automobiles, aerospace, and high-end machine tools.
4. Wide application
Angular contact ball bearings are widely used in various industrial fields due to their excellent performance. They are particularly outstanding in high-load environments such as high-speed spindles, gearboxes, precision machine tools, automobile engines, and aerospace equipment. These applications often require bearings to have good load-bearing capacity and wear resistance to cope with harsh working conditions and long-term operation. For example, in the machine tool industry, high-speed rotating spindles need to bear huge radial and axial loads. The design of angular contact ball bearings can effectively share these loads and ensure the accuracy and stability of machine tools. In the automotive field, angular contact ball bearings are used in components such as drive shafts and wheel hubs, which improves the performance and safety of automobiles. With the advancement of technology, the materials and manufacturing processes of angular contact ball bearings are also constantly improving, making them more adaptable and reliable in more high-load and high-speed occasions.
5. Maintenance and Care
Although angular contact ball bearings perform well under high loads, proper maintenance and care are still the key to ensure their long-term stable operation. Users should regularly check the lubrication status of the bearings, and the lubricating oil or grease should be replaced in time according to the operating conditions to prevent wear caused by poor lubrication. It is recommended to develop a detailed maintenance plan, including regular inspection, lubrication and replacement, to ensure that the bearings are always in optimal condition. Monitoring the operating temperature and vibration of the bearings is also an important maintenance measure. Excessive temperature may be a sign of insufficient lubrication or bearing damage, while abnormal vibration may indicate internal failure. For high-load applications, it is particularly important to note that operators should follow the manufacturer's instructions for use and avoid overloading or misuse to avoid unnecessary damage to the bearings. Through reasonable maintenance and care, users can effectively extend the service life of angular contact ball bearings and ensure the safe and efficient operation of equipment under high load conditions.