+86-574 86567814
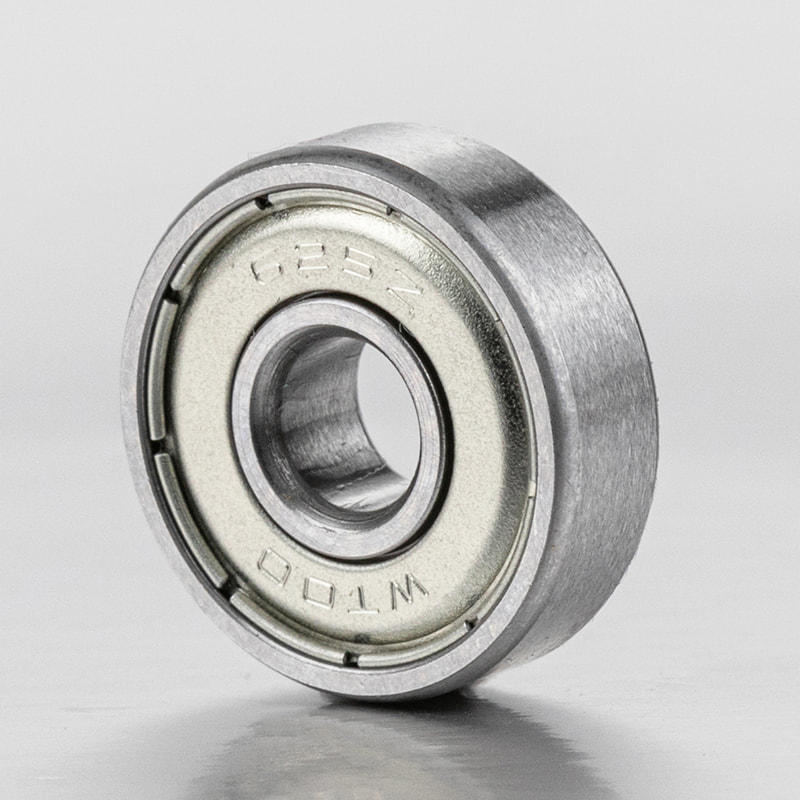
625-Super quiet, high precision, long life deep groove ball bearings
Deep groove ball bearings Deep groove ball bearing...
View moreDeep groove ball bearings Deep groove ball bearing...
View moreDeep groove ball bearings Deep groove ball bearing...
View moreDeep groove ball bearings Deep groove ball bearing...
View more1.Lubrication Issues: Proper lubrication is crucial for the smooth operation and longevity of deep groove ball bearings. Without adequate lubrication, friction between the rolling elements and raceways increases, leading to overheating and premature wear. Insufficient lubricant also fails to effectively distribute loads within the bearing, causing localized stress concentrations that can result in surface damage or spalling. Additionally, using the wrong type or grade of lubricant can degrade performance and accelerate wear. Regular monitoring of lubricant condition and replenishment according to manufacturer recommendations is essential to mitigate lubrication-related failures.
2.Contamination: Contaminants such as dirt, dust, water, and chemicals can infiltrate deep groove ball bearings, compromising their performance and lifespan. Even minute particles can cause abrasive wear, particularly in high-speed applications where they become trapped between rolling elements and raceways. Moisture ingress can lead to corrosion of bearing surfaces, while chemical contaminants can degrade lubricant properties and accelerate deterioration. Effective sealing and shielding mechanisms, along with regular cleaning and maintenance practices, are necessary to prevent contamination-related failures.
3.Misalignment: Proper alignment of shafts and housings is critical to ensure uniform loading and prevent excessive stress on deep groove ball bearings. Misalignment can occur due to assembly errors, thermal expansion, or structural deflections in machinery. As a result, the bearing experiences uneven loading, causing localized stress concentrations that accelerate fatigue and wear. Over time, misalignment can lead to premature failure of bearing components, such as raceway brinelling or ball indentation. Regular alignment checks and corrective measures are essential to minimize the risk of misalignment-induced failures.
4.Overloading: Deep groove ball bearings are designed to withstand specific axial and radial loads within their rated capacities. Exceeding these limits can lead to overloading, causing deformation, plastic flow, or fracture of bearing components. Overloaded bearings may exhibit symptoms such as increased noise, vibration, or excessive heat generation. Continued operation under such conditions can accelerate wear and compromise bearing integrity, ultimately resulting in catastrophic failure. Proper selection of bearings based on anticipated loads, along with regular monitoring of operating conditions, is necessary to prevent overloading-related failures.
5.Improper Installation: Correct installation procedures are vital to ensure the proper functioning and longevity of deep groove ball bearings. Improper fitting, seating, or alignment during installation can introduce stress concentrations or distortions in bearing components, compromising their integrity. Over-tightening mounting bolts or applying excessive force during assembly can cause brinelling or raceway damage. Conversely, loose fits can result in fretting corrosion or axial displacement under operational loads. Following manufacturer guidelines and employing appropriate tools and techniques are essential to minimize the risk of installation-related failures.
6.Fatigue: Fatigue failure occurs in deep groove ball bearings due to repeated cyclic loading and unloading of bearing components. This phenomenon is particularly prevalent in high-speed or high-load applications where rolling elements experience alternating stress cycles. Over time, microcracks propagate within bearing components, leading to surface spalling, flaking, or fracture. Factors such as material properties, operating conditions, and maintenance practices influence the rate of fatigue accumulation. Regular inspection, lubrication, and replacement of worn bearings help mitigate the risk of fatigue-induced failures and extend bearing life.
7.Poor Maintenance: Neglecting routine inspection and maintenance practices can accelerate the deterioration of deep groove ball bearings, leading to premature failure. Lack of lubricant replenishment, inadequate cleaning, or ignoring early warning signs of wear can exacerbate existing issues and compromise bearing performance. Additionally, deferred replacement of worn bearings increases the likelihood of catastrophic failures, resulting in costly downtime and potential equipment damage. Implementing a proactive maintenance schedule, including periodic lubrication, cleaning, and condition monitoring, is essential to prolong bearing life and prevent avoidable failures.
8.Material Defects: Deep groove ball bearing components are manufactured to stringent quality standards to ensure durability and reliability. However, defects in material composition or manufacturing processes can compromise the structural integrity of bearings, leading to premature failure. Common material defects include inclusions, voids, or metallurgical anomalies that weaken bearing components and promote crack initiation. Quality control measures, such as material testing and inspection protocols, help mitigate the risk of material-related failures. Additionally, sourcing bearings from reputable manufacturers with established quality assurance practices can minimize the likelihood of encountering material defects.
9.High Temperatures: Elevated operating temperatures pose significant challenges to deep groove ball bearings, as they accelerate wear, degrade lubricant properties, and promote thermal expansion of bearing components. Excessive heat generation can result from frictional losses, overloading, or insufficient cooling in the application environment. Prolonged exposure to high temperatures can cause thermal degradation of bearing materials, leading to reduced hardness, increased dimensional instability, or metallurgical changes. Employing heat-resistant materials, optimizing lubrication, and implementing effective cooling measures are essential strategies to mitigate the detrimental effects of high temperatures and prolong bearing life.
10.Excessive Speed: Deep groove ball bearings are designed to operate within specified speed limits based on factors such as ball size, cage design, and lubrication type. Operating bearings at speeds beyond these limits can induce dynamic instabilities, such as skidding, sliding, or ball spinning, leading to increased friction, heat generation, and wear. Excessive speeds also exacerbate centrifugal forces acting on rolling elements, causing them to undergo plastic deformation or fatigue failure. Proper selection of bearings based on application requirements, along with adherence to recommended operating speeds, is crucial to prevent speed-induced failures and ensure reliable performance.
635-Super quiet, high precision, long life deep groove ball bearings
Deep groove ball bearings are widely used bearing type and are particularly versatile. They have low friction and are optimized for low noise and low vibration which enables high rotational speeds. They accommodate radial and axial loads in both directions, are easy to mount, and require less maintenance than other bearing types.