+86-574 86567814
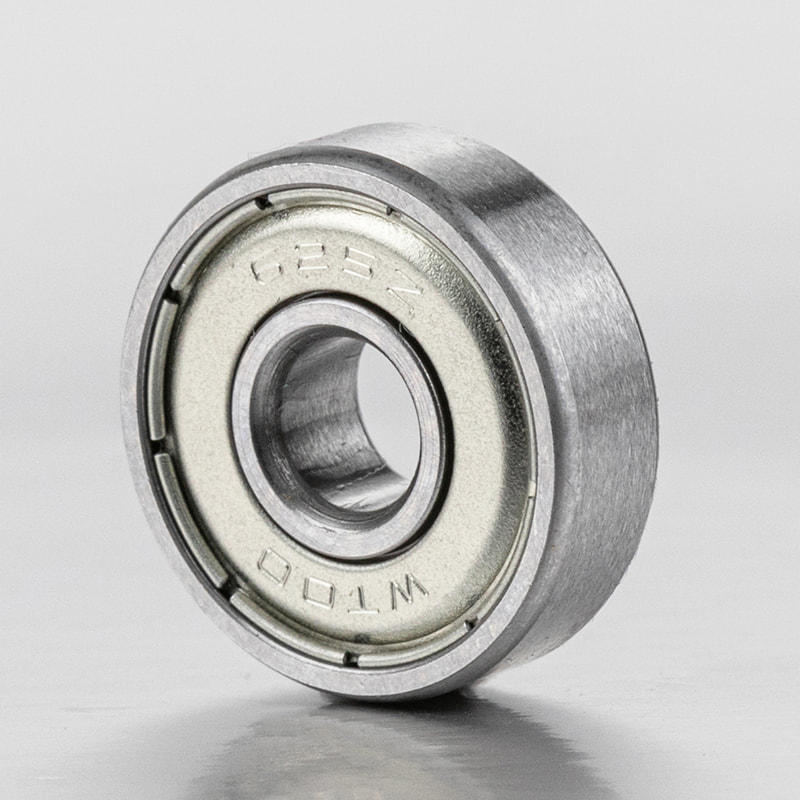
625-Super quiet, high precision, long life deep groove ball bearings
Deep groove ball bearings Deep groove ball bearing...
View moreDeep groove ball bearings Deep groove ball bearing...
View moreDeep groove ball bearings Deep groove ball bearing...
View moreDeep groove ball bearings Deep groove ball bearing...
View moreAngular contact ball bearings are designed with an inner and outer ring raceway that is displaced relative to each other along the bearing axis. This design feature enables the bearing to manage combined loads, meaning it can handle both radial (perpendicular to the shaft) and axial (along the shaft) loads at the same time. This dual-load capability is particularly beneficial in industrial machinery where machines experience complex loading conditions. For example, in machine tool spindles, gearboxes, and other precision-driven machinery, the ability to support both types of loads simultaneously enhances the performance and efficiency of the equipment.
One of the most significant advantages of angular contact ball bearings is their ability to carry large axial loads, which increases as the contact angle between the ball and raceways becomes larger. The contact angle is the angle formed between the line joining the points of contact and a line perpendicular to the bearing axis. A larger contact angle allows the bearing to carry higher axial loads, making it a preferred choice for applications with substantial axial forces. For instance, in heavy-duty industrial machinery such as turbines, gearboxes, and automotive components, where axial forces are predominant, angular contact ball bearings are particularly effective. This feature ensures that the machinery can withstand higher operational pressures, improving the overall load-bearing capacity and ensuring the longevity of the components.
In addition to their excellent load-carrying capabilities, angular contact ball bearings also offer superior precision and accuracy. Their precise design allows them to operate with minimal friction, resulting in smooth and stable rotation. This characteristic is essential for applications requiring high-speed motion or tight tolerance requirements. For example, in the aerospace, automotive, and robotics industries, angular contact ball bearings are used in components that demand high rotational accuracy and minimal deviation. The smooth operation and low friction also contribute to reduced heat generation, which helps prevent wear and extends the lifespan of the bearing, further enhancing its reliability.
Another notable benefit of angular contact ball bearings is their durability and long service life. Since these bearings are specifically designed to handle both radial and axial loads, they are less prone to failure under heavy operational stresses compared to other bearing types. Their robust construction allows them to perform reliably even in harsh operating conditions, such as in extreme temperatures, high-speed applications, or environments with heavy vibrations. This durability is particularly beneficial in industries where machinery is required to run continuously, minimizing downtime and reducing the need for frequent maintenance. The longevity of these bearings contributes to the overall efficiency and cost-effectiveness of the machinery they are used in, as businesses can reduce the frequency of repairs and replacements.
Angular contact ball bearings are also known for their ability to handle high-speed operations. Their design minimizes friction and heat buildup, allowing them to operate at higher speeds without compromising their performance. This makes them ideal for applications such as electric motors, pumps, turbines, and other high-speed machinery where maintaining constant speed is essential. The ability to handle high rotational speeds also improves the overall efficiency of the machine, as it allows the machinery to perform at optimal levels without the risk of overheating or excessive wear.