+86-574 86567814
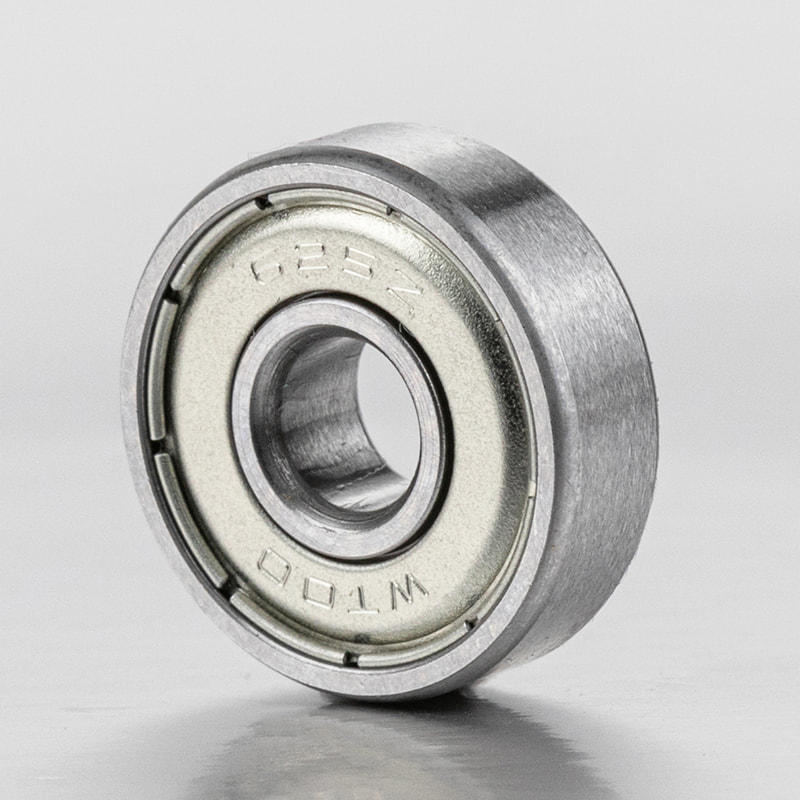
625-Super quiet, high precision, long life deep groove ball bearings
Deep groove ball bearings Deep groove ball bearing...
View moreDeep groove ball bearings Deep groove ball bearing...
View moreDeep groove ball bearings Deep groove ball bearing...
View moreDeep groove ball bearings Deep groove ball bearing...
View moreThe reason why angular contact ball bearings show significant advantages in combined load (coexistence of radial and axial loads) scenarios is due to their unique design philosophy and deep coupling of mechanical properties. This type of bearing does not simply adjust the angle of the structure of the deep groove ball bearing, but through a series of precise geometric and material design, it realizes active control of complex load paths, thus becoming an irreplaceable core component in industrial scenarios with high speed, high precision and high rigidity requirements.
From the perspective of geometric structure, the contact angle between the raceway and the steel ball of the angular contact ball bearing (usually 15°, 25° or 40°) is the core feature that distinguishes it from other bearings. The existence of the contact angle essentially changes the force transmission path - when the axial load is applied, the contact point between the steel ball and the raceway is not perpendicular to the axis, but forms a pressure distribution along the inclined direction of the contact angle. This inclined contact surface decomposes the axial force into two components, radial and axial, and at the same time, through the optimized design of the raceway curvature radius (the outer ring raceway is usually deeper than the inner ring), the load is more evenly distributed between the rolling elements. For example, in a bearing with a contact angle of 25°, the axial load that a single rolling element can withstand can reach more than 50% of its radial load capacity, while the axial load capacity of a traditional deep groove ball bearing is often less than 20% of the radial load capacity. This mechanical vector decomposition capability enables angular contact bearings to avoid stress concentration on the edge of the raceway when facing the cutting force (radial) and feed thrust (axial) generated by the high-speed rotation of the machine tool spindle, thereby significantly extending the service life.
A deeper level of performance improvement comes from the dynamic rigidity design of the bearing system. When angular contact ball bearings are installed in pairs in a back-to-back (DB) or face-to-face (DF) manner, the precise application of preload not only eliminates the internal clearance, but also builds a closed-loop force flow network inside the bearing group. Taking the CNC machine tool spindle as an example, when the two sets of bearings configured back-to-back rotate at high speed, the preload will form a stable elastic deformation field between the inner and outer rings, which has a "buffering" effect on changes in external loads. When the spindle is subjected to sudden radial cutting force, the rigid support of the preload structure can control the deformation to the micron level, thereby ensuring the smoothness of the machined surface; when subjected to axial feed force, the inclined raceway of the contact angle will convert part of the axial load into radial expansion force, and achieve internal force balance through the interaction of paired bearings. This mechanical coupling effect makes the stiffness of the angular contact bearing group under combined load more than 300% higher than that of the single-row deep groove ball bearing.
The collaborative innovation of materials science and lubrication technology further amplifies its performance advantages. The raceway surface of modern angular contact ball bearings is often made of carburized steel or ceramic coating (such as silicon nitride), and its surface hardness can reach more than HRC60. At the same time, the raceway roughness is controlled within Ra 0.05μm through superfinishing process. This extreme smoothness not only reduces the rolling friction coefficient, but more importantly, it can suppress the micro-slip phenomenon between the steel ball and the cage caused by centrifugal force under high-speed conditions (such as the speed of turbocharger bearings often exceeds 200,000rpm). In terms of lubrication, the combination of fully synthetic PAO base oil and lithium complex soap thickener can form an elastic fluid dynamic oil film with a thickness of only 0.1-0.3μm in the contact area. When the bearing is subjected to a combined load, this nano-scale oil film will experience a surge in viscosity in the high-pressure area of the contact ellipse (up to 3-4GPa), thus forming a solid-like protective layer between the steel ball and the raceway. For example, in aerospace actuators, this lubrication mechanism allows the bearing to maintain stable friction characteristics in an extreme temperature range of -54°C to 180°C.