+86-574 86567814
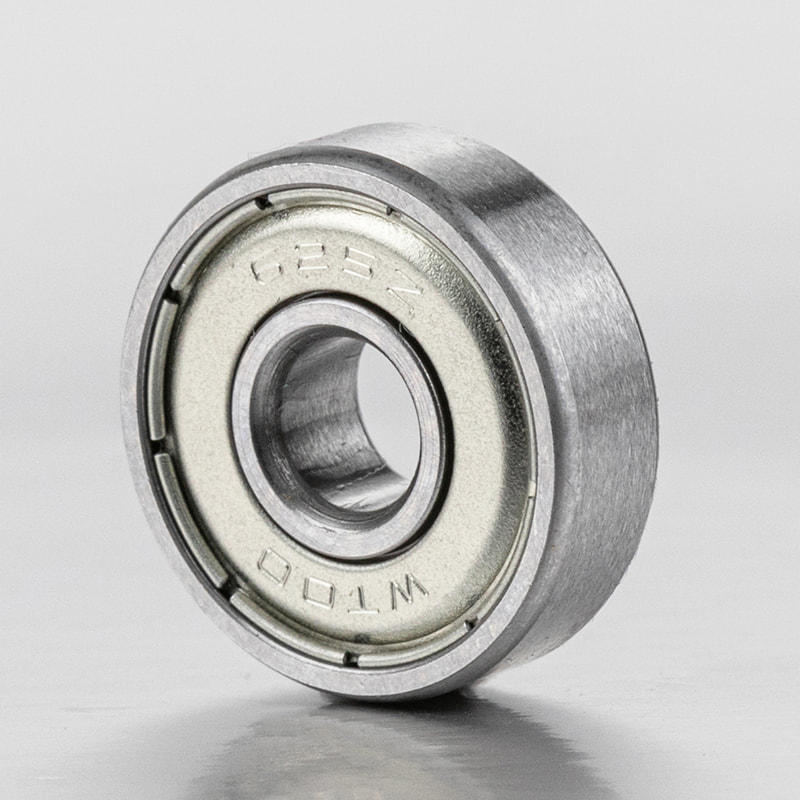
625-Super quiet, high precision, long life deep groove ball bearings
Deep groove ball bearings Deep groove ball bearing...
View moreDeep groove ball bearings Deep groove ball bearing...
View moreDeep groove ball bearings Deep groove ball bearing...
View moreDeep groove ball bearings Deep groove ball bearing...
View more1. Enhanced Accuracy and Precision
Accuracy and precision are the cornerstone of many industrial applications, from CNC machines to robotics, where even a slight deviation can lead to significant errors and costly rework. Ball screw bearings are designed with tight tolerances that ensure precise linear motion with minimal deviation. Unlike traditional lead screws, which rely on sliding friction, ball screw bearings use rolling balls, reducing friction and wear. This feature translates into smoother motion, greater control, and less room for error.
In CNC machinery, for example, ball screw bearings ensure that the machine's axes move exactly as instructed, with minimal backlash (the small gap between the nut and screw). In processes like precision machining, aerospace manufacturing, or semiconductor fabrication, a tiny error can result in defective parts. With ball screw bearings, however, high-precision movement is achieved, which is vital when working with components requiring tolerances of micrometers or less. This high degree of accuracy ensures that machines can consistently perform complex tasks, ensuring product quality and reducing the need for manual adjustments.
2. High Efficiency and Load Capacity
One of the primary advantages of ball screw bearings over traditional mechanical systems is their superior efficiency. Ball screws use rolling elements (balls) instead of sliding friction surfaces, which significantly reduces energy loss and the heat generated during operation. This efficiency makes ball screw bearings ideal for applications that demand high load capacities with minimal energy consumption, such as in high-performance machinery, automotive systems, or industrial robots.
The efficiency of ball screw bearings also means they can operate at higher speeds while maintaining smooth motion. This is particularly important in high-throughput manufacturing systems where machines must process large quantities of parts without compromising on speed or precision. Ball screw bearings are capable of supporting higher axial loads compared to lead screws or other linear motion systems. This makes them ideal for applications that require heavy-duty performance, such as in lifting systems, actuators, or large-scale industrial machines. Their ability to carry high loads without excessive friction or energy loss contributes significantly to the efficiency of precision machinery, which is a critical factor in increasing production rates and reducing operational costs.
3. Reduced Friction and Heat Generation
Friction is one of the biggest challenges in mechanical systems, particularly in high-speed, high-load applications. Excessive friction not only reduces the efficiency of the machine but can also lead to heat buildup, which accelerates wear and reduces the lifespan of the components. Ball screw bearings significantly mitigate this issue by using balls that roll instead of sliding, drastically reducing friction and, in turn, the heat generated during operation. This reduction in heat generation is particularly beneficial in precision machinery, where maintaining consistent operating conditions is essential for optimal performance.
In applications such as CNC machining or injection molding, heat buildup can lead to dimensional inaccuracies, degraded part quality, and premature failure of components. Ball screw bearings, with their low friction properties, help maintain temperature stability within the system, ensuring that the machinery continues to operate within the desired tolerance ranges. The reduced friction minimizes the wear and tear on both the bearing and the surrounding components, extending the overall lifespan of the system. This results in less downtime for maintenance and fewer costly repairs, making ball screw bearings a cost-effective solution for industries where precision and reliability are paramount.
4. Improved Durability and Longevity
Ball screw bearings are built to last, thanks to their design that minimizes friction and wear. Unlike traditional lead screws or other linear motion systems, which can suffer from significant wear over time due to constant sliding contact, ball screw bearings rely on rolling elements that distribute the load evenly across the contact surface. This design reduces the wear on the bearing surfaces and helps prevent the premature failure of components, especially under heavy loads or extended use.
In precision machinery, such as medical equipment or aerospace systems, where machine uptime is critical, the durability of the ball screw bearing plays a pivotal role in ensuring long-term, trouble-free operation. The extended lifespan of ball screw bearings reduces the frequency of maintenance or part replacements, which can be costly and time-consuming. These bearings help maintain the accuracy of the machinery over time, which is crucial in industries where precision is required for safety, functionality, or quality control. In applications that demand high reliability and consistency, such as in robotics or semiconductor manufacturing, the durability of ball screw bearings ensures that the machines continue to perform at peak levels throughout their operational lifespan.
5. Minimal Backlash for Higher Precision
Backlash is the slight movement or "play" that occurs when the direction of motion is reversed, which can lead to inaccuracies in positioning. In precision machinery, even the smallest amount of backlash can compromise the quality of the final product, especially in applications such as 3D printing, milling, or laser cutting. Ball screw bearings are engineered to minimize backlash, providing highly accurate and repeatable motion. The rolling balls within the bearing assembly reduce the gap between the nut and the screw, which means less room for play, even when the direction of motion is reversed.
For machines that require exact positioning, such as in the production of micro-components or in automated assembly lines, minimizing backlash is critical to achieving the desired accuracy. Ball screw bearings with preloaded systems can further reduce backlash by applying a constant force between the nut and screw, ensuring that the bearing remains in tight contact without any looseness. This ability to achieve high precision with minimal backlash is a key reason why ball screw bearings are so commonly used in industries where exact replication of movement is required, such as in aerospace, medical device manufacturing, and high-precision automation systems.
6. Versatility Across Industries
Ball screw bearings are widely used across various industries due to their versatility and ability to perform under diverse operating conditions. In manufacturing, they are essential for precise motion control in CNC machines, robotics, and automation systems. The versatility of ball screw bearings makes them applicable in industries ranging from automotive and aerospace to medical equipment and semiconductor manufacturing. In the automotive sector, for example, ball screw bearings are used in electric steering systems, where precision and reliability are critical for safety and performance. Similarly, in aerospace applications, these bearings provide the accuracy needed for the control systems of aircraft, where even the slightest error can have serious consequences.
Ball screw bearings are also used in medical devices that require fine motion control, such as in surgical robots, where they help achieve the high precision needed for minimally invasive procedures. In the semiconductor industry, ball screw bearings play a critical role in wafer processing equipment, where extreme accuracy and smooth motion are necessary for the production of microchips. The adaptability of ball screw bearings to different operational requirements and environments has made them a standard choice in any industry where precise, high-performance motion is required. Their broad range of applications across various sectors highlights their importance in precision machinery.