+86-574 86567814
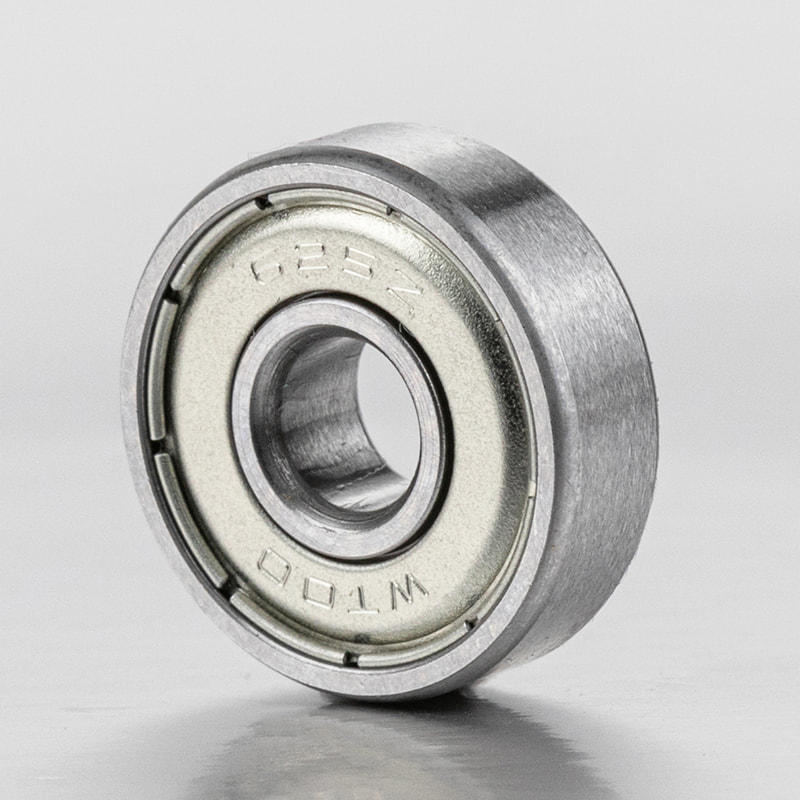
625-Super quiet, high precision, long life deep groove ball bearings
Deep groove ball bearings Deep groove ball bearing...
View moreDeep groove ball bearings Deep groove ball bearing...
View moreDeep groove ball bearings Deep groove ball bearing...
View moreDeep groove ball bearings Deep groove ball bearing...
View morePrecision angular contact ball bearings are vital components in the high-performance machinery sector, especially in applications like machine tool spindles and high-frequency motors. These bearings are specifically designed to meet the demanding needs of these systems, The unique characteristics of precision angular contact ball bearings make them ideal for such applications, offering multiple benefits that enhance the efficiency, performance, and longevity of machine tool spindles and high-frequency motors.
Machine tool spindles and high-frequency motors are constantly subjected to both radial and axial loads during operation. Radial loads arise when the load is applied perpendicular to the bearing shaft, while axial loads are applied along the shaft's axis. Precision angular contact ball bearings are engineered to accommodate these combined loads simultaneously, which is a significant advantage over traditional deep groove ball bearings that can only handle radial loads. The design of these bearings features an angular contact between the ball and the raceway, which allows them to effectively support both types of load without compromising the stability of the system. This capability is especially important for machine tool spindles, where precision is critical, as well as for high-frequency motors that must operate smoothly under varying loads.
Another key characteristic of precision angular contact ball bearings is their ability to perform efficiently at high speeds. Machine tool spindles and high-frequency motors often operate at rotational speeds that generate significant friction and heat. Bearings with high friction can lead to energy loss, excessive wear, and overheating, which can ultimately reduce the performance and lifespan of the equipment. Precision angular contact ball bearings are designed with a low coefficient of friction, minimizing resistance and allowing for smoother rotation even at high speeds. This enables machine tool spindles and high-frequency motors to operate efficiently, without generating excessive heat or wasting energy, thus improving overall system performance and reducing operating costs.
In industries where precision machining is required, such as CNC machining or high-speed motors, the accuracy of every movement is crucial to producing high-quality outputs. Precision angular contact ball bearings are manufactured with very tight tolerances, ensuring that the balls and raceways are perfectly matched and the bearing runs smoothly without any wobble or play. This level of precision is essential in machine tool spindles, where even the smallest deviation can result in machining errors or poor-quality parts. Similarly, in high-frequency motors, where high-speed rotation is combined with the need for precise control, the accuracy provided by these bearings ensures the motor runs at optimal performance.
Durability is another important factor that makes precision angular contact ball bearings indispensable for machine tool spindles and high-frequency motors. These systems often run for extended periods, sometimes in harsh environments or under heavy loads, and require bearings that can withstand such conditions without failing prematurely. Precision angular contact ball bearings are known for their longevity, as they are manufactured to high standards of quality, with the ability to endure both high speeds and heavy loads. Their robust design reduces the frequency of maintenance and replacement, minimizing downtime and repair costs, which is a crucial consideration in industrial operations where machine availability is a priority.
Heat resistance is also a vital characteristic for bearings used in high-speed applications like machine tool spindles and high-frequency motors. When bearings operate at high speeds, the friction generated between the balls and raceways leads to heat buildup, which can degrade the performance of the bearing and the overall system. Precision angular contact ball bearings are designed to handle elevated temperatures, particularly when using high-performance materials like ceramic balls or advanced lubricants. This heat resistance ensures that the bearings maintain their efficiency even under extreme conditions, making them ideal for applications where heat generation is inevitable.
The versatility of precision angular contact ball bearings is another reason for their widespread use in machine tool spindles and high-frequency motors. These bearings are highly customizable, with variations in contact angles, materials, and retainers to suit specific operational requirements. For instance, machine tool spindles may require bearings with a specific contact angle to optimize load handling, while high-frequency motors may require bearings with ceramic balls to reduce friction further and increase speed capabilities.